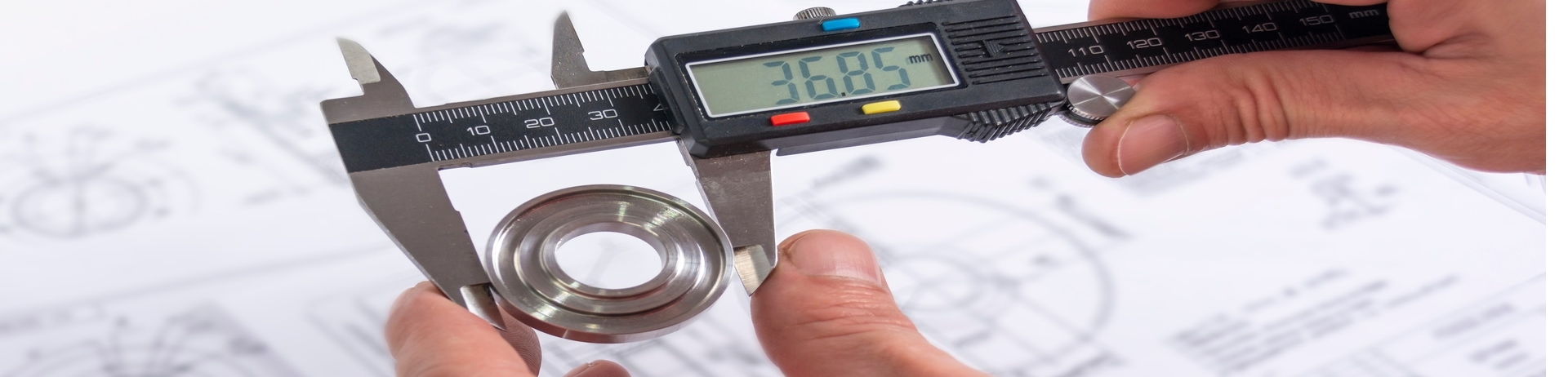
Initial Production Check
Case Study - Quality Implications of a Pet Chew Toy with Sound Function
Third Party Inspection
This case study involves the quality inspection of 26,928 pieces within 374 cartons of Dog chew balls equipped with a whistle sound feature.
During the inspection, each product underwent simulated squeezing and sound testing as below video.
After five compressions, it was observed that 10% of the products experienced issues with the thin membrane inside the whistle (photos 2&3), leading to detachment or inhalation (photo 4). This resulted in the blockage of the sound hole and considerable instability in the sound function (photos 5&6).
The issue was reported to the factory, explaining that they had procured the sound devices from another supplier without conducting in-house testing. The situation significantly affected the primary functionality of the product, necessitating a comprehensive rework of all the items.
This case underscores the far-reaching impact of quality concerns on a product. It highlights the importance of meticulous component procurement and thorough pre-production testing by factories. Our mission is to deliver high-quality products, and this requires collaborative efforts between factories and suppliers to ensure that all products meet customer expectations. Through proactive quality control, we can preempt functional issues and maintain our customers' trust and satisfaction.
- Improving Product Quality With HKQ.C. Center Audits
- Case Study - Quality Control in Wooden Products before Shipped from Guangdong
- How Our Quality Control Audits Benefit Your Firm
- Case Study - A Lesson in Bamboo Fencing Inspection
- The Top Reasons to Choose Our Third Party Inspection Services
- Case Study - Manufacturing Discrepancy in Pet Ladders
- How to Choose the Right China Product Inspection Service for Your Business
- Case Study - Unyielding Commitment to Testing Standards