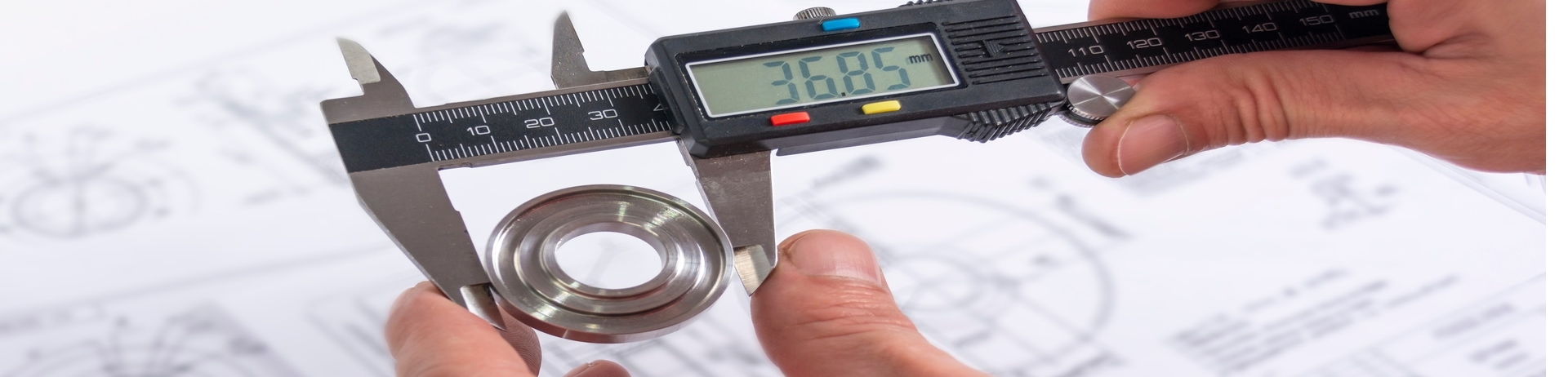
Initial Production Check
Case Study - Scrutinizing a Scratched Situation during inspection
Third Party Inspection
In this case, we received a pre-inspection notification from the factory, stating that production was 100% complete. However, upon arrival, the inspector found only 50% of the products were ready. These products were black plastic toys, prone to visible scratches. What shocked the inspector was that the factory hadn't taken any protective measures during production. The products were left exposed on the production line without proper packaging. When they couldn't be packaged immediately, they were carelessly stacked, causing scratches and collisions.
When the inspector expressed concern about the need for better product protection, the factory claimed this was their standard practice. However, the inspector questioned why this consistent approach hadn't addressed the issue of scratches.
Upon closer inspection, it was evident that 100% of the products displayed scratches, a problem overlooked in previous reports provided by the client. The inspector documented this issue. The factory, although initially resistant, had no choice but to deal with it post-inspection.
This case underscores the importance of timely updates to product information to maintain market competitiveness and consumer trust, even in seemingly minor details. At our inspection company, we strive to be the bridge that helps clients avoid potential claims by ensuring products meet the highest quality standards and accurately represent their condition.
- Case Study - A Lesson in Bamboo Fencing Inspection
- Case Study - Discovered Hangtag Print Residue during Pre-shipment Inspection
- Case Study - Attention to Detail - Snap Button Issue in Skiwear Accessories
- Case Study - Ensuring Precise Product Compatibility in Handcrafted Artifacts
- Cost-effectiveness of Third-party Inspection Services
- Case Study - The Significance of Quality Control and Effective Communication: Unveiling the Story Behind Transparency Issue
- Case Study - Decisive Differences in Barcodes and Model Numbers
- Quality Control Inspection Services